In the figure below, the datasheet for recycled PE 100 granules is shown. It is 100% recycled. For more information, you can download the datasheet.
Recycled PE100- Datasheet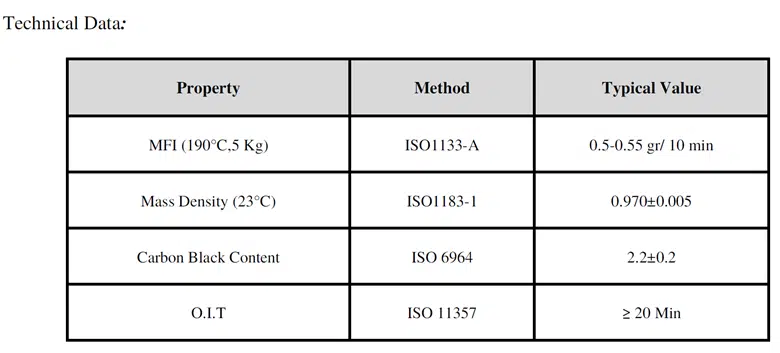
If you have a proposed percentage for producing this material and require it from us, please let us know. We can produce and supply it with the best method, materials, and quality.
Introduction:
Polyethylene is one of the most prominent raw materials used in the production of pipes for water supply networks, sewage systems, gas distribution, irrigation, fluid transfer systems, and industrial wastewater. It is also utilized in pressurized irrigation networks and mobile irrigation systems. Due to its unique properties such as corrosion resistance, low weight, considerable flexibility, and excellent hydrostatic characteristics, polyethylene is currently considered a cost-effective and reliable solution for many pipeline applications.
The minimal strength needed at 20 degrees Celsius and for 50 years after installation is the basis for classifying different kinds of materials used in the building of polyethylene pipes. The table below shows the many varieties of polyethylene that have been utilized in pipes over time.
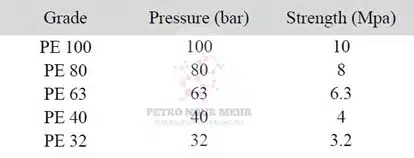
Figure 1: Characteristic of various types of polyethylene pipes.
History of Polyethylene Pipes:
Polyethylene pipes were first used in the 1950s as pressure pipes, based on low-density polyethylene with designations such as PE 32, PE 40, and PE 63. This generation of pipes was susceptible to cracking due to stress and pressure. They also had poor resistance to cracks and their growth. However, despite these issues, these pipes were lighter and easier to transport compared to lightweight metallic systems, and they did not have the corrosion problems present in metal pipes. Nevertheless, these pipes had a high weight and thickness for suitable applications, leading to increased production costs.
To address the challenges posed by this generation, a medium-density material called PE 80 was introduced. It would be possible to create pipes with thinner walls and adequate strength by making the material denser. As a result, the final product has a lower weight and a higher-pressure tolerance. The reduction in wall thickness also led to increased flow capacity and output, which had economic benefits. The expectation was that further increases in density would bring further improvements in properties. In this regard, PE 80 found its way into the polyethylene pipe production industry. This product introduced unique physical and performance characteristics, combining higher density with lower weight and thickness, providing increased pressure tolerance. Today, this type of polyethylene is widely used in pipe production.
Pipe Production Process:
The diagram below illustrates the extrusion method used to manufacture polyethylene pipes. Raw materials in the form of granules are introduced into the extruder and melt due to heat. The molten materials are then pushed forward by a screw and, after exiting the extruder, enter the mold. After coming out of the mold, the molten materials go into the diameter adjuster (vacuum tank), where the right amount of pressure is applied to shape them. As soon as the pipe leaves the diameter adjuster, layers of cold water flow to cool its surface.
The produced polyethylene pipes are gradually drawn through vacuum tanks and coolers using a pulling device. With a marking device, technical specifications, production date, standard mark, and the abbreviated mark of the company are
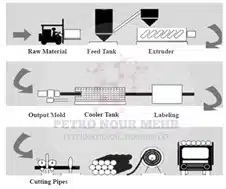
Figure 2 : The production stages of polyethylene pipes.
recorded on the pipe. Subsequently, the pipes are cut into various predetermined lengths using a cutting device.
Double-screw and single-screw extruders are the most common types of machines used for pipe production. The speed and shape of the screw, mixing speed, and the mold pressure of the extruder determine the output of the extruder. The resulting product must be controlled and compliant with standards at all production stages.
Tests and Common Standards in Assessing the Quality and Performance of Pipes:
Melt Flow Index (MFI):
According to ISO 1133, the Melt Flow Index (MFI) test measures the melt flow rate of materials at a constant temperature and time to look at how the materials behave inside the extruder. This test is performed on the final product as well as the raw materials to determine the quality of the materials. The standard states that there should be no more than a 2% difference between the product’s MFI and the raw material’s MFI.
Carbon Percentage Determination:
The ISO 18553 and ISO 6964 standards are followed in determining the carbon content of raw materials and final products. In order to do this, a predetermined volume of raw materials is pyrolyzed in a furnace with pure nitrogen at 800 degrees Celsius. The amount of carbon remaining after oxygen combustion is consumed in order to calculate the proportion of ash (additive materials) in the given initial sample.Top of Form
The allowable carbon percentage in polyethylene pipes ranges from 2 to 5.2% by weight and should be uniformly distributed throughout the pipe. In regions where carbon accumulation exceeds the permissible percentage, stress concentration occurs, making the pipe susceptible to damage. Conversely, where the carbon content falls below the allowable limit, the pipe’s resistance to UV stress decreases.
Hydrostatic Pressure Test:
The hydrostatic pressure test, performed according to Iranian National Standards 1-12181 and 2-12181, assesses the product’s strength against hydrostatic pressures. In this test, pipe samples are submerged in a water tank at a constant internal pressure for 100 hours at 20 degrees Celsius, 165 hours at 80 degrees Celsius, or 1000 hours at 80 degrees Celsius. The emergence of any defects in the samples (cracking, ballooning, localized swelling, leakage, and hairline cracks) indicates product failure.
Dimensional Measurement and Visual Inspection of Pipes:
When polyethylene pipes are tested in accordance with Iranian National Standard 10610, they must be free from any internal and surface roughness, defects, or voids. Partial deformities are acceptable as long as they do not reduce the thickness below the permissible limit.
Oxidation Induction Time (OIT) Test:
The Oxidation Induction Time (OIT) test, according to Iranian National Standard 6-7186, is conducted on raw materials to determine their thermal stability. According to the standard, the destruction time should not be less than 20 minutes.
Global Production of Polyethylene Pipes:
The global market value of heavy polyethylene-based pipes reached 3.18 billion dollars in 2022, and from 2023 to 2032, an annual growth rate of 9.4% is anticipated. It is expected that this market will reach 5.29 billion dollars by 2032. The tremendous rise in HDPE pipe demand for gas and water transmission worldwide is one of the primary drivers of the polyethylene pipe market’s expansion. The Middle East emerged as the leading manufacturer of HDPE pipes among pipe-producing nations in 2022, holding a 5.43% market share. For instance, Two of the major Middle Eastern producers of pipes are WL Plastics Corporation (www.wlplastics.com) and Supreme Industries Limited (www.supreme.co.in).
Among the Asian nations, Iran made a substantial contribution to this market share. The following figure provides a summary of the released statistics.
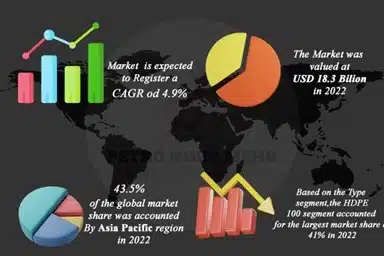
Figure 3 : The market size of Polyethylene Pipe granules (PE100) in 2022
Recycling Cycle of Polyethylene Pipes:
After using polyethylene pipes, considering the properties and characteristics of polymer materials, these pipes can be recycled and reintroduced into the production cycle. In this section, we will examine the recycling process of polyethylene pipes carried out by the Petro Nour Mehr group.
Recycling polyethylene pipes consists of five main sections: collection, separation, milling, washing, and granulation. We will now delve into the analysis and explanation of these mentioned stages.
Pipe Collection:
The first stage in recycling polyethylene pipes is the collection of the pipes. In this stage, polyethylene pipes used in various industries such as oil and gas, agriculture, etc., are gathered. These pipes are sold in the market in industrial range. Industrial pipes, usually with high volume and suitable quality, are put up for sale by organizations and large manufacturers. The usage period of these pipes is very short, or sometimes due to process issues during production, they have failed to meet the required standards, making them eligible for recycling. This kind of pipes, allowing us to provide high-quality and suitable products to customers. The below picture shows the pipes that we use for recycling.
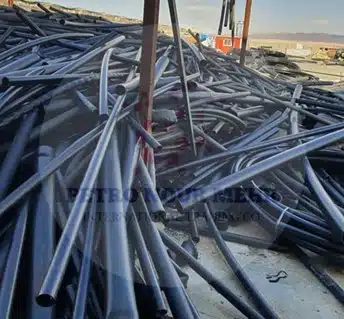
Figure 4: An example of recycled polyethylene pipes at the Petro Nour Mehr Company
Separation:
After collecting the pipes, considering that polyethylene pipes are used in various industries, and each industry produces these pipes with specific standards and specifications that have unique properties, these pipes need to be separated from each other. For example, pipes for gas and fluid transmission should be separated from pipes for water transmission and recycled separately. In the Petro Nour Mehr group, these pipes are meticulously separated from each other, and any contaminants on these pipes are completely removed.
Milling:
After separating the pipes based on their application and quality, these pipes are transformed into smaller pieces using a milling machine to facilitate the washing and granulation process. Therefore, the pipes are crushed into finer pieces using a milling machine. The image below shows the milling machine available in the facility.
mine the recycling process of polyethylene pipes carried out by the Petro Nour Mehr group.
Recycling polyethylene pipes consists of five main sections: collection, separation, milling, washing, and granulation. We will now delve into the analysis and explanation of these mentioned stages.
Pipe Collection:
The first stage in recycling polyethylene pipes is the collection of the pipes. In this stage, polyethylene pipes used in various industries such as oil and gas, agriculture, etc., are gathered. These pipes are sold in the market in industrial range. Industrial pipes, usually with high volume and suitable quality, are put up for sale by organizations and large manufacturers. The usage period of these pipes is very short, or sometimes due to process issues during production, they have failed to meet the required standards, making them eligible for recycling. This kind of pipes, allowing us to provide high-quality and suitable products to customers. The below picture shows the pipes that we use for recycling.
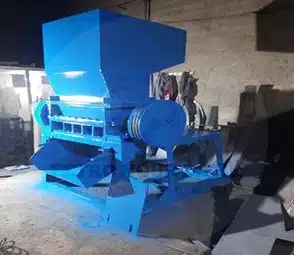
Figure 5: The milling machine present in the Petro Nour Mehr Company for grinding polyethylene pipes.
Washing:
To clean the pipes from any potential impurities, the washing process is performed on the milled pipes. The milled pipes are placed inside a water tank and, with the help of water pressure and blades inside the tank, are directed forward. The length of the washing tank is adjusted based on the level of contamination and impurities present on the pipes. After thorough washing of the milled materials, a heater or a centrifuge (high-speed rotation device) is used to remove water and dry the materials.
Granulation:
After washing and drying the milled pipes, they are transferred to the granulator machine, where they are melted using an extruder and transformed back into granules. After the granulation process, these materials are reintroduced into the production cycle. Granulator machines can be single-screw or twin-screw, with single-screw granulators being more common. The produced granules can have a strand or pellet shape. The image below shows the molten material exiting the extruder and a sample of the produced granules at Petro Nour Mehr facility.
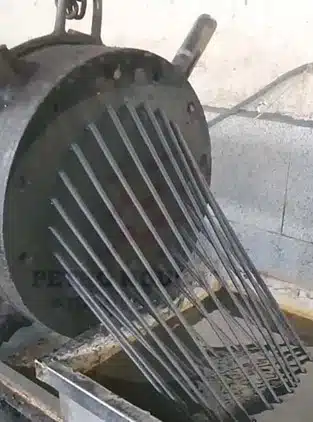
Figure 6: Molten and extruded polyethylene strands from the granulator machine.
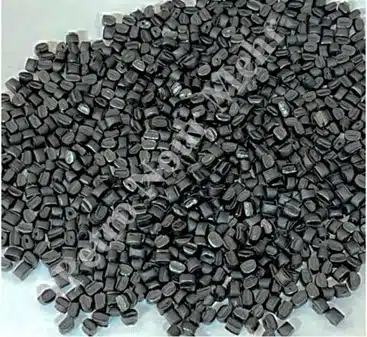
Figure 7: Polyethylene granules produced at the Petro Nour Mehr Company
Important Notes on Recycled Pipe Granules:
There are crucial considerations regarding recycled pipe granules that need attention. One of the most significant issues is the unpleasant odor emitted by recycled granules, which customers often complain about. The cause of the odor in recycled granules can be attributed to the following reasons:
- If the granules produce a burnt smell, it may be due to an increase in the temperature of the granulator machine or extruder. The elevated temperature reduces viscosity, leading to an increased output from the machine. However, this phenomenon results in the granules having a burnt smell.
- If the output has a smell of cleaning agents, it could be caused by the use of contaminated waste materials, such as detergent bottles. This contamination can cause the output to carry the smell of cleaning agents. Additionally, the use of contaminated materials may result in the produced granules having bubbles, indicating the presence of contaminated waste.
Another crucial consideration in the production of recycled pipe granules is the precise classification of these materials, as well as the milling and washing processes. This is because metal fasteners and seals are often used to secure water transmission pipes and agricultural pipes. These materials must be completely separated during the milling and washing processes, as their presence can cause irreparable damage to the granulator machine.
Product Analysis:
After the production of granules, all granules undergo analysis in reputable laboratories in Iran to examine their properties. Essential analyses, including Melt Flow Index (MFI), density, and Oxidation Induction Time (OIT), are performed on the samples.